Case history
Support and project development from 3D files to silicone molds, production, and assembly of the first prototype.
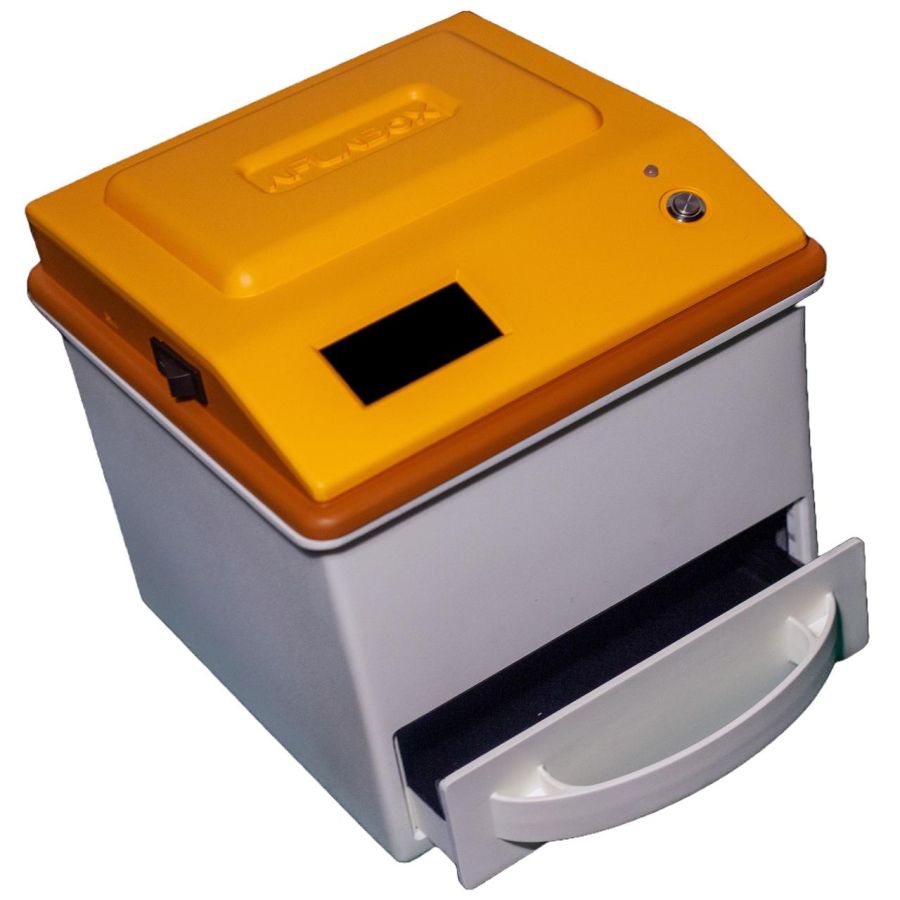
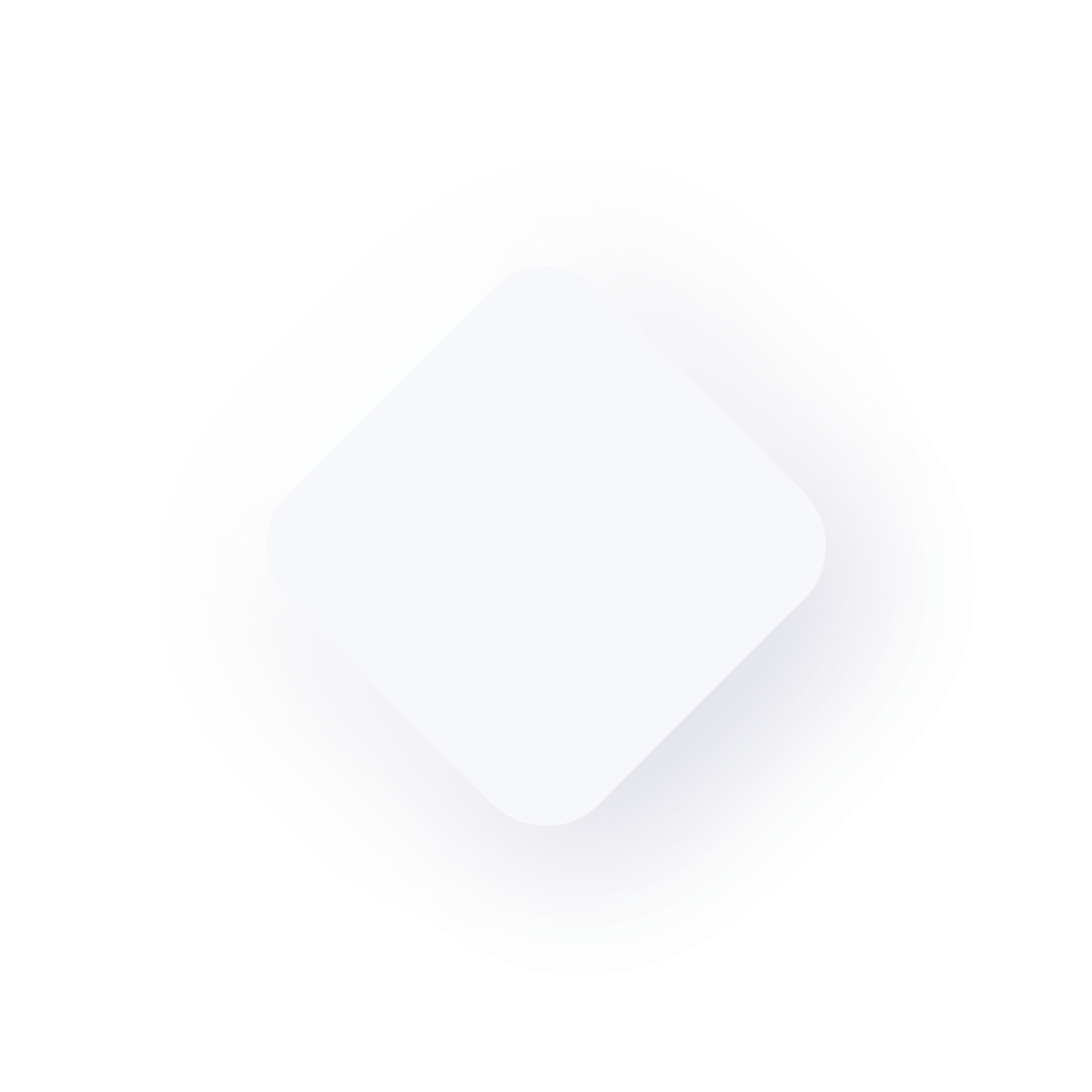
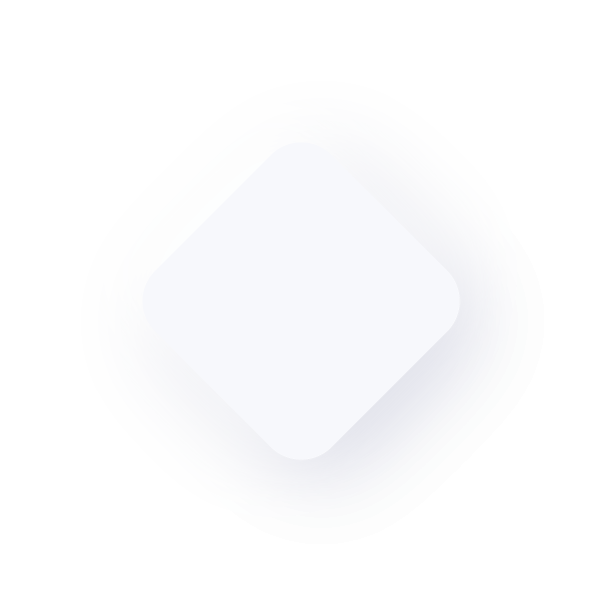
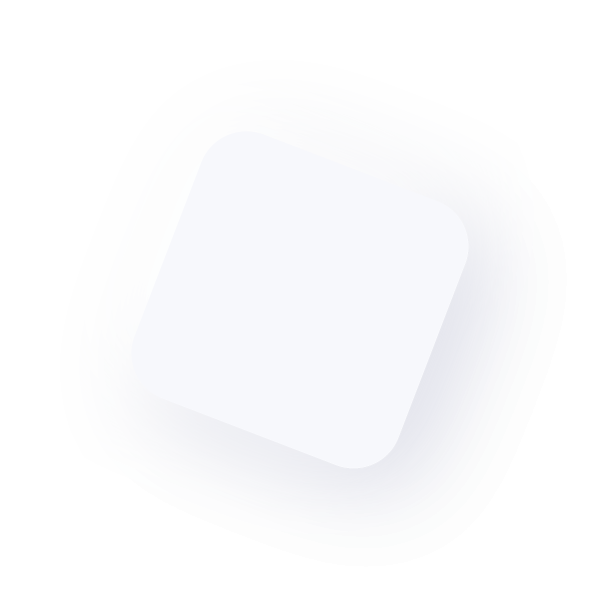
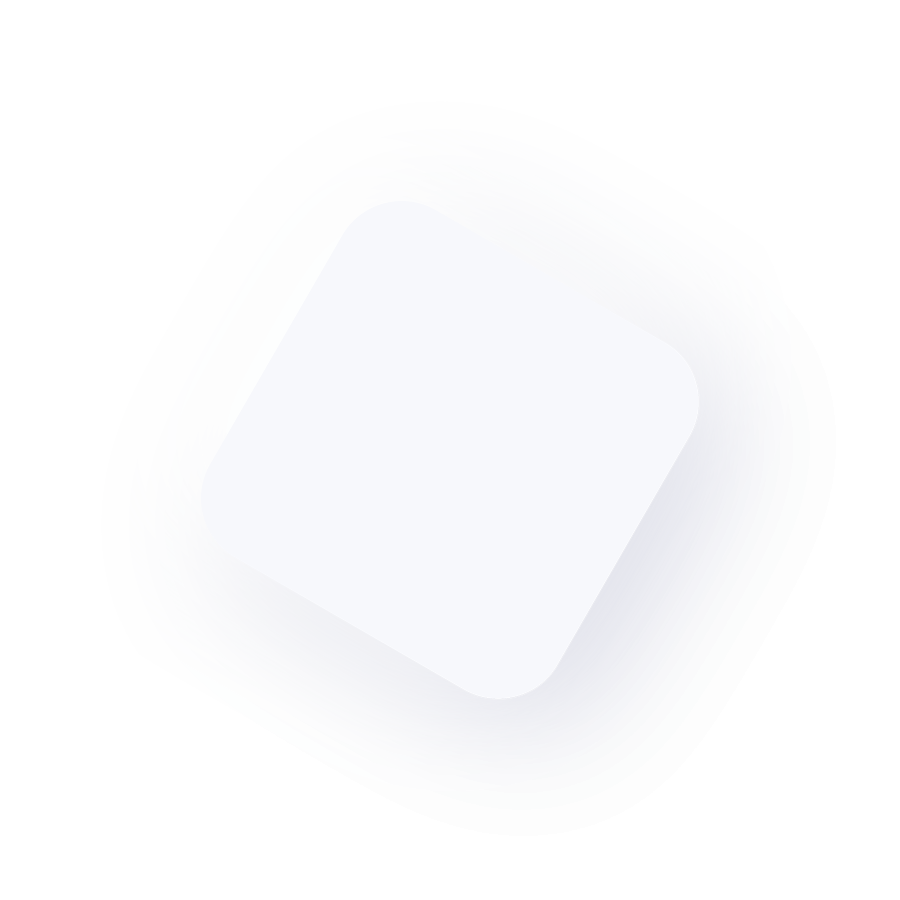
CASE STUDY:
Support and project development from 3D files to silicone molds, production, and assembly of the first prototype.
CLIENT:
Startup operating in food safety and laboratory analysis.
THE CHALLENGE:
To develop a food safety device for analyzing cereals, starting from a client-provided design.
VPLAST SOLUTION:
After an initial feasibility analysis, we completely redesigned the client’s drawings to meet their requirements, as the materials provided were not suitable for injection molding.
The client needed to control costs and produce an initial small batch of components for presentation to investors and global organizations involved in the project, as well as to test and verify functionality after assembly.
We proposed producing the components using silicone molds, allowing for cost control while creating functional components for testing and display. These molds, unlike steel molds, have a limited lifespan but enable the production of a few pieces at lower costs and shorter creation timelines.
Once the various box components were produced, we proceeded with the assembly, delivering the finished product to the client.
CLIENT BENEFITS:
- Vplast acted as the sole reference partner throughout all project phases.
- Cost reduction compared to 3D printing.
- Shorter production timelines.