Injection Molding
Choose Vplast: Your Partner for Bringing Your Project to Life
Injection molding is a plastic processing technique that allows for the continuous and rapid production of a large number of parts in various shapes, using thermoplastic polymers. These polymers can vary depending on the desired technical performance.
With injection molding, we can manufacture products for a wide range of industries, including automotive, electrical, and electronics, where we excel in technical expertise and deliver the highest levels of precision.
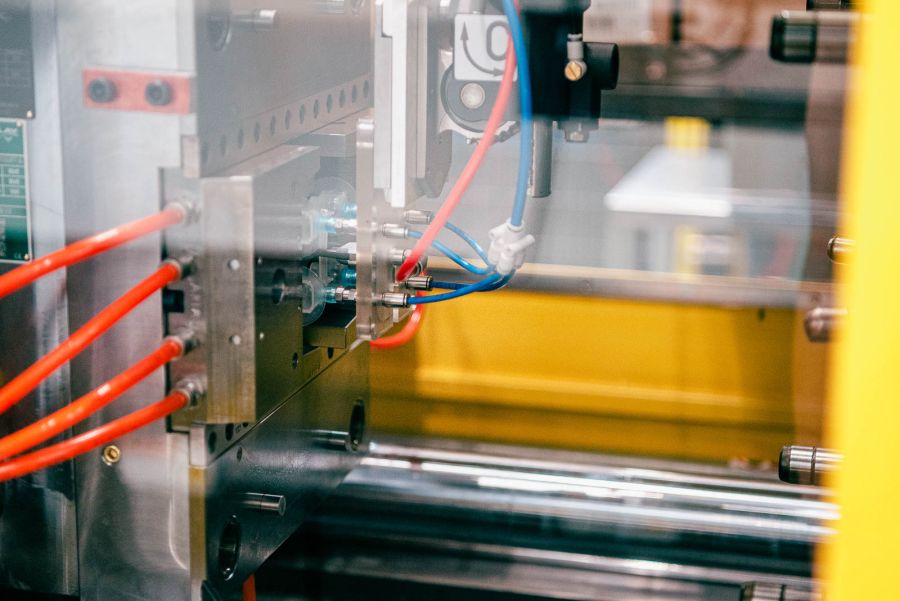
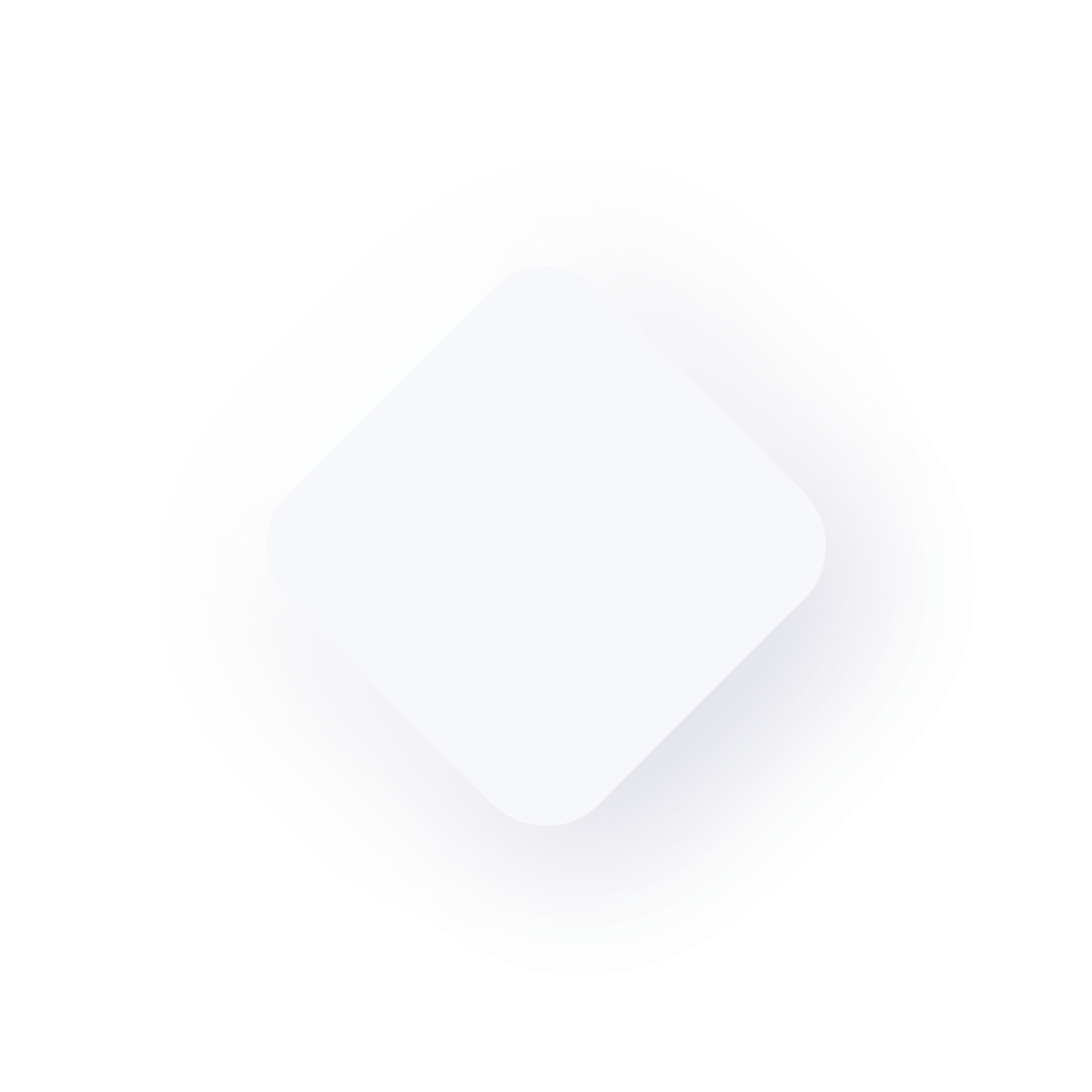
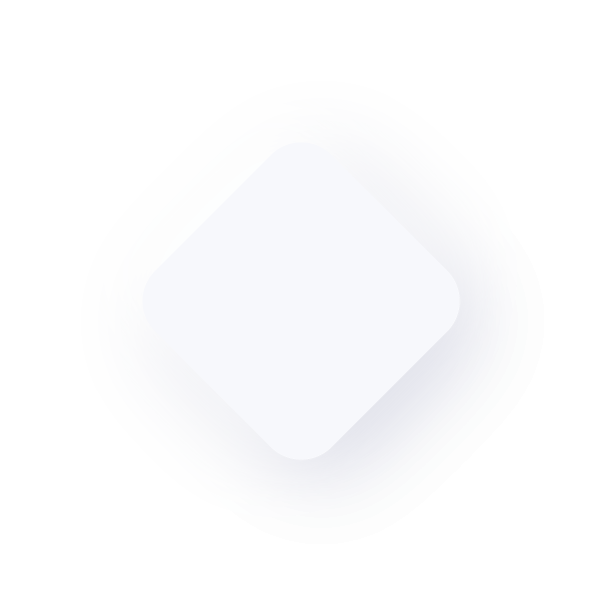
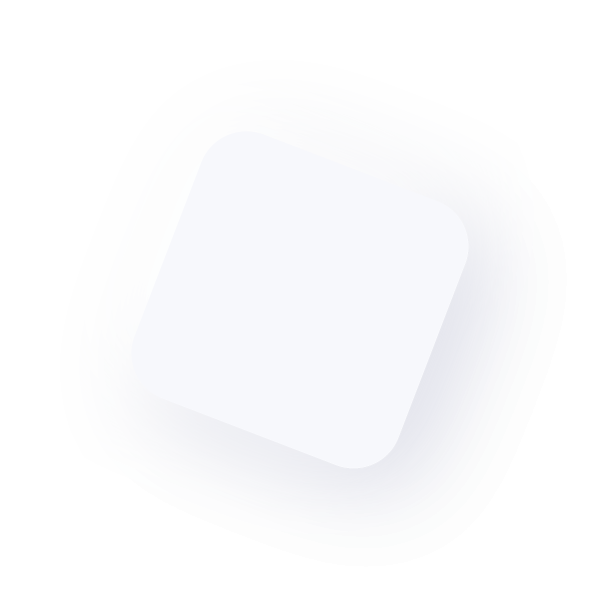
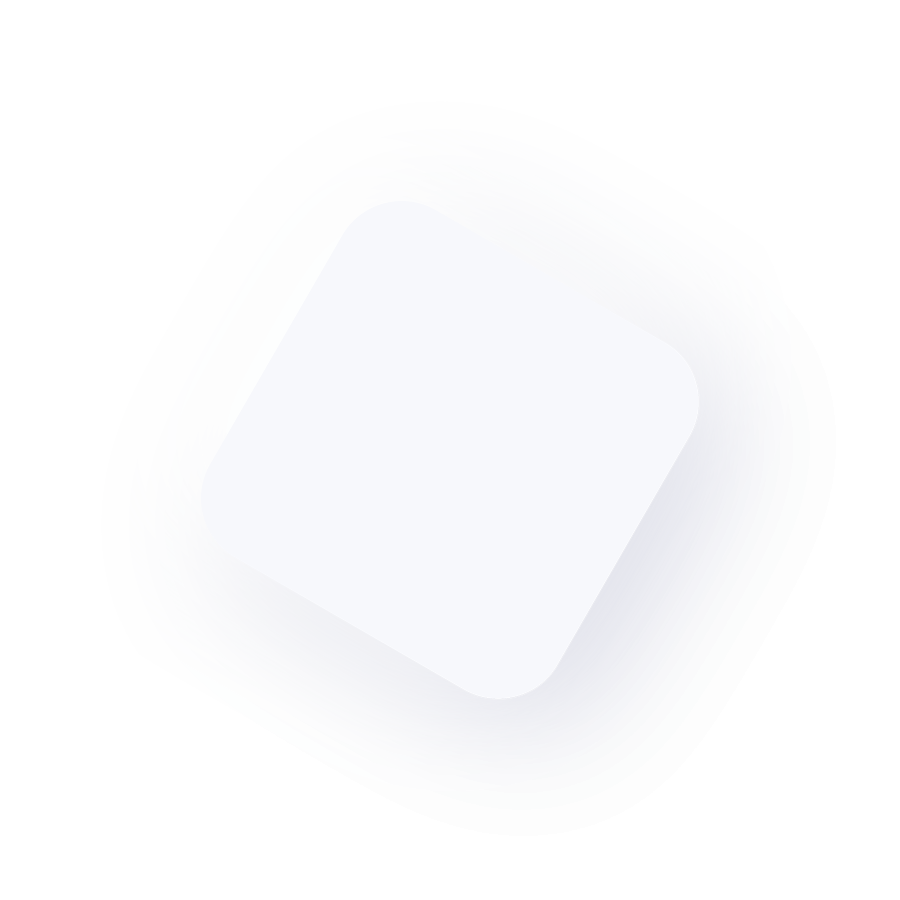
The plastic injection molding process
The stages of injection molding
The plastic injection molding cycle enables the production of molded parts that are ready for delivery to the customer or for further processing, starting from plastic granules. The production cycle includes the following micro-phases.

STEP 1 - Preparation of materials
The plastic injection molding cycle allows for the production of molded parts that are ready for delivery to the customer or further processing, starting from plastic granules. The production cycle includes the following micro-phases.

STEP 2 - Machine setup
Properly trained operators perform the mechanical process of installing the mold into the press suitable for production.

STEP 3 -Feeding Plastic Granules into the Injection Unit
After preparation, the granules are fed into the press's plasticizing screw through a hopper, using a gravity-fed system.

STEP 4 - Material Loading into the Plasticizing Screw
Depending on the type of raw material, the mold, and the technical specifications of the product, production managers set the parameters for proper material handling, including melt temperature, charging speed, and retraction settings.
In this phase, the rotating screw pulls the material from the hopper and melts it, transforming it into a viscous state, ready for the next stage.

STEP 5 - Injection and Holding Pressure
Injection speed, pressure, switchover point, holding time, and holding pressure are set to ensure the molten material correctly fills the mold cavities. These parameters are critical for preventing defects such as incomplete fills, burns, and flash.

STEP 6 - Cooling the Material in the Mold
During this phase, the molten material solidifies, taking the shape of the specifically designed mold. Cooling times vary depending on the type of polymer used and the shape of the part being produced. This step is crucial to ensure the component maintains the correct dimensions.

STEP 7 - Mold Opening and Part Ejection
Once the molten plastic has solidified, the mold opens, and its ejection system releases the newly molded part.

STEP 8 - Manual or Automated Part Retrieval
A robot or one of our operators (in the case of manual handling) retrieves the molded part for packaging or to proceed to any subsequent processing stages.
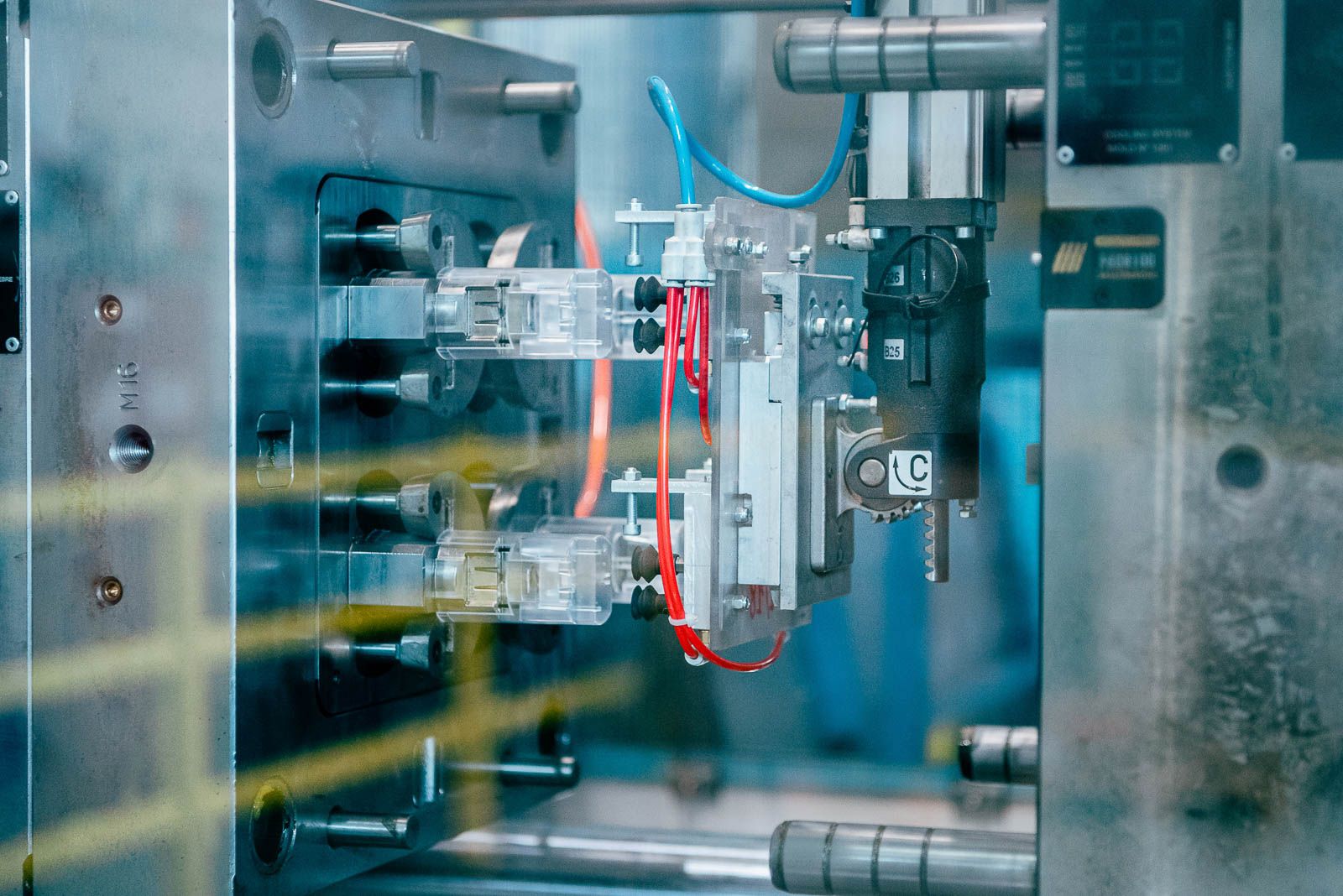
The Advantages of Injection Molding
Through advanced technology and the constant pursuit of new raw materials, more and more injection-molded components are replacing metal parts, offering both lighter weight and superior performance.
A wide variety of polymers and engineering plastics designed to ensure the required technical performance.
Continuous and fast production of parts in various, even complex, shapes.
Production of small-sized parts.
High productivity and process automation.
Know how, innovation and integrated process control in molding
Our in-depth knowledge of materials and over 30 years of experience in plastic injection molding ensure an excellent plastic processing workflow, certified by ISO 9001 standards.
Over the years, we have introduced new technologies and advanced integrated process control systems. Today, our machinery for molding plastic components features a high level of automation, including fully electric presses. These presses deliver maximum precision, reduced production times, increased production capacity, and low energy consumption.
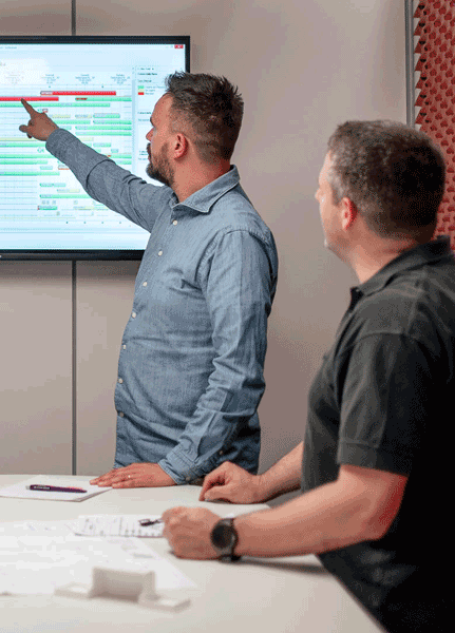
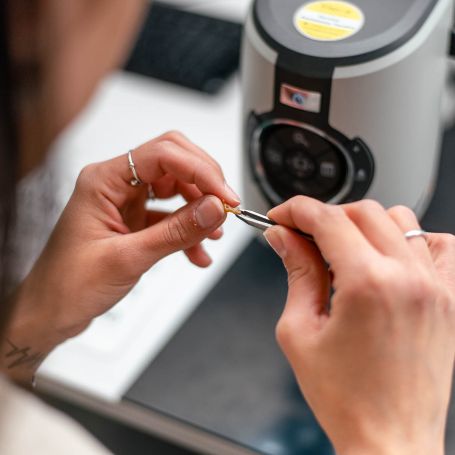
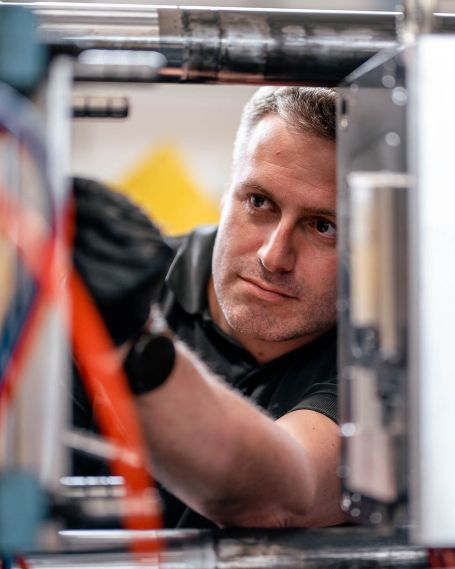
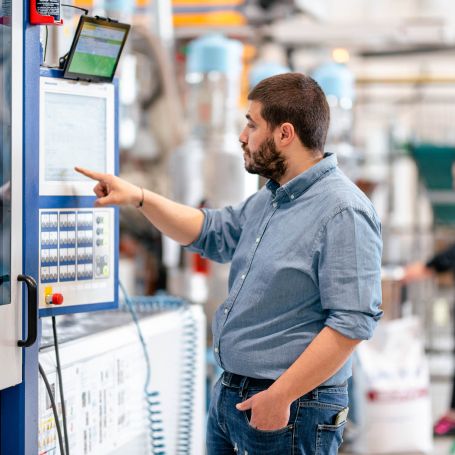
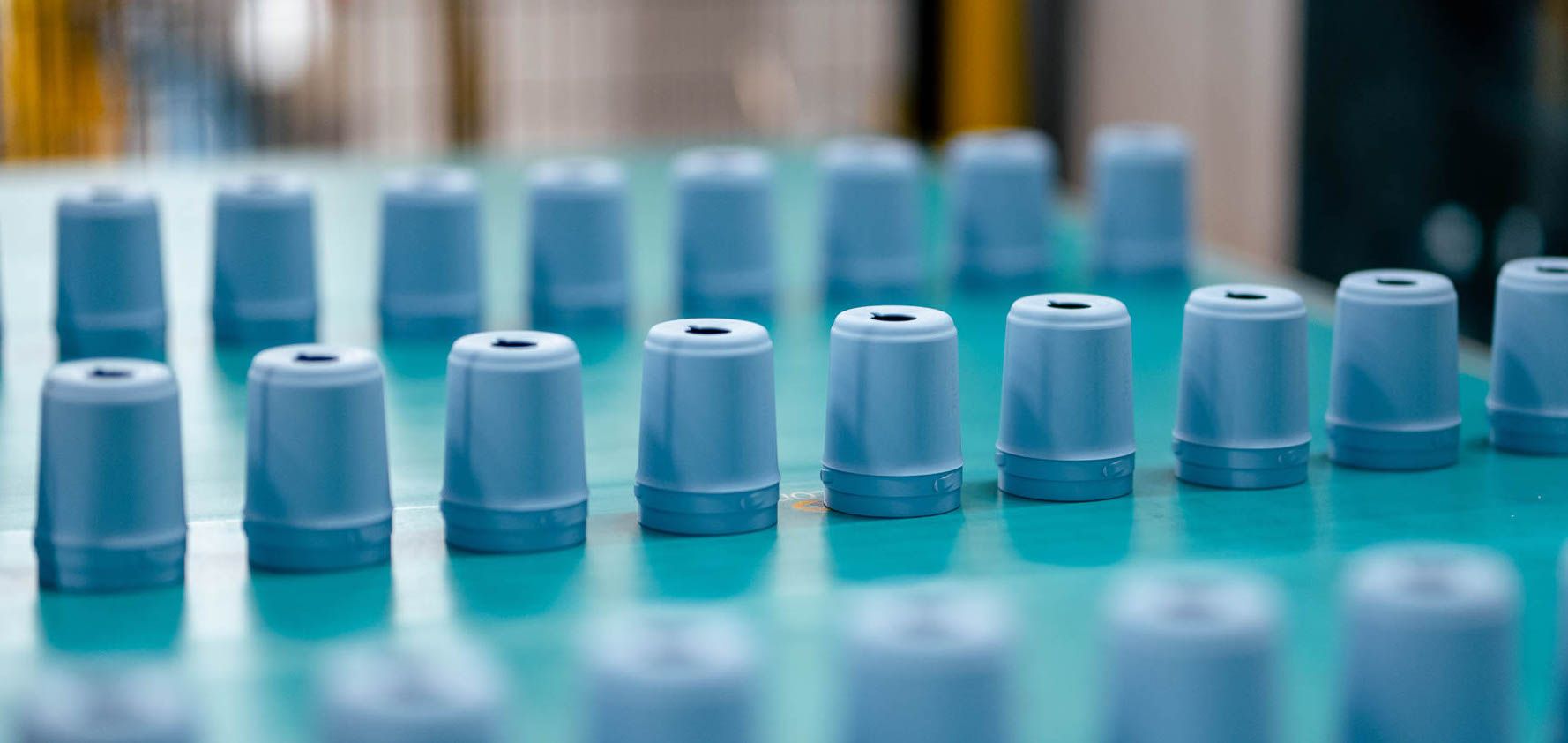
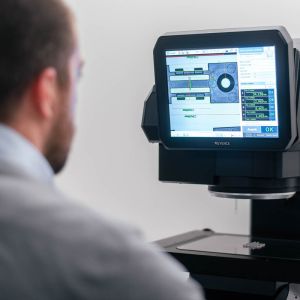
Customized product molding
Thanks to our developed technical expertise, we can accurately understand and meet our clients' needs, delivering functional and high-performing plastic technical components that align with their expectations.
Our organizational structure and collaboration with trusted designers and mold makers allow us to respond swiftly and flexibly to client requirements, whether standard or customized. We offer a comprehensive consulting service, guiding and supporting clients from the initial concept on paper to the final molded, assembled, packaged, and delivered product.
Tell Us About Your Project.
Let’s develop it together.
Let’s develop it together.