Case history
Reducing Mold Costs
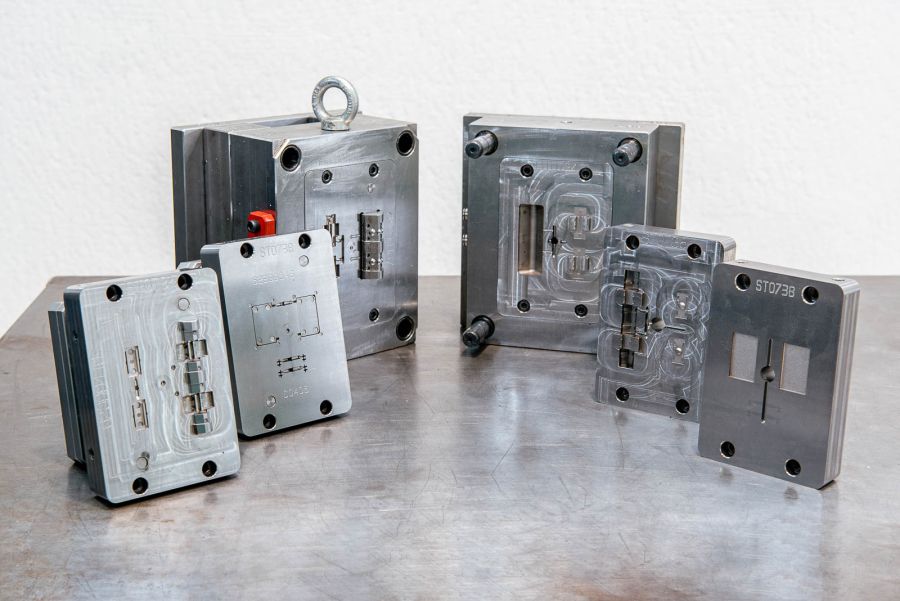
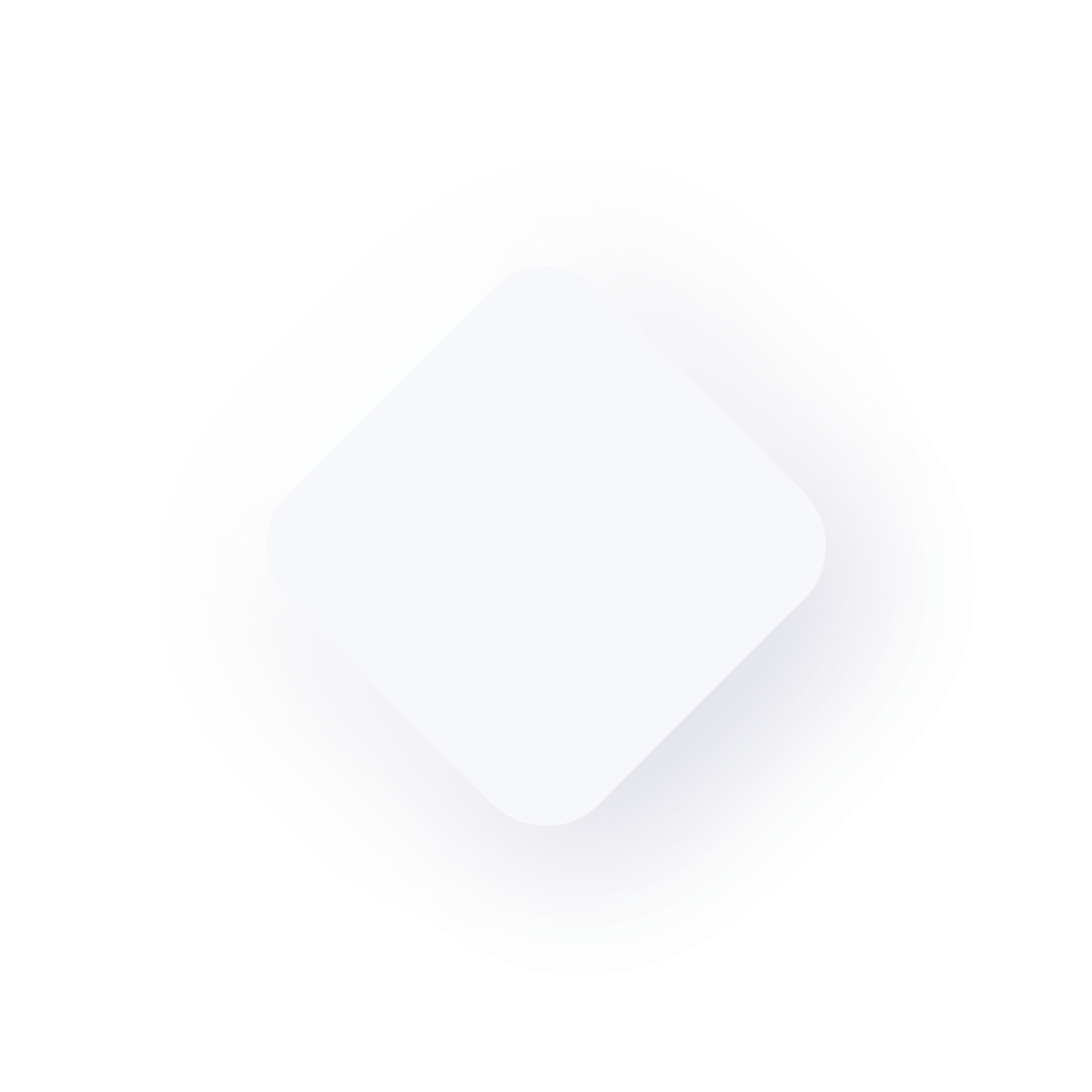
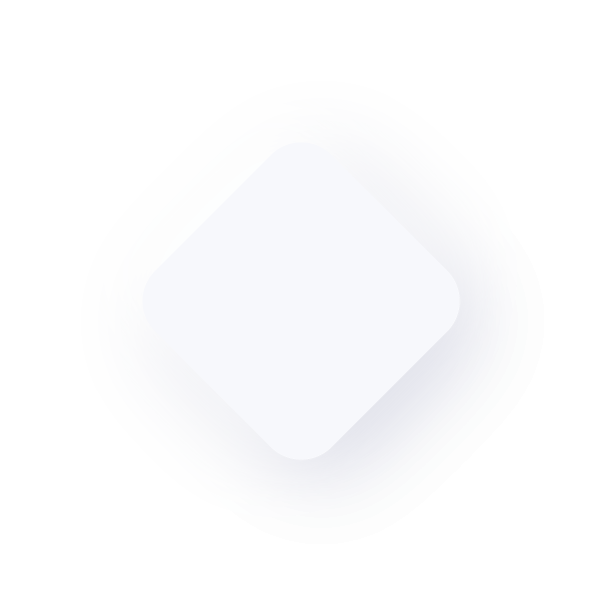
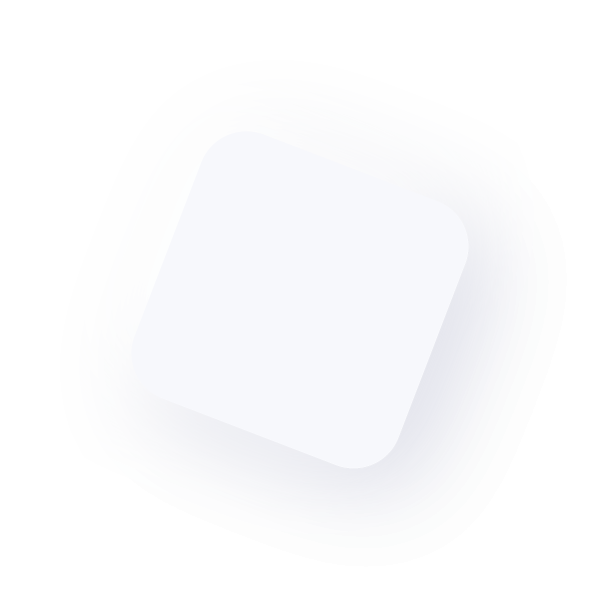
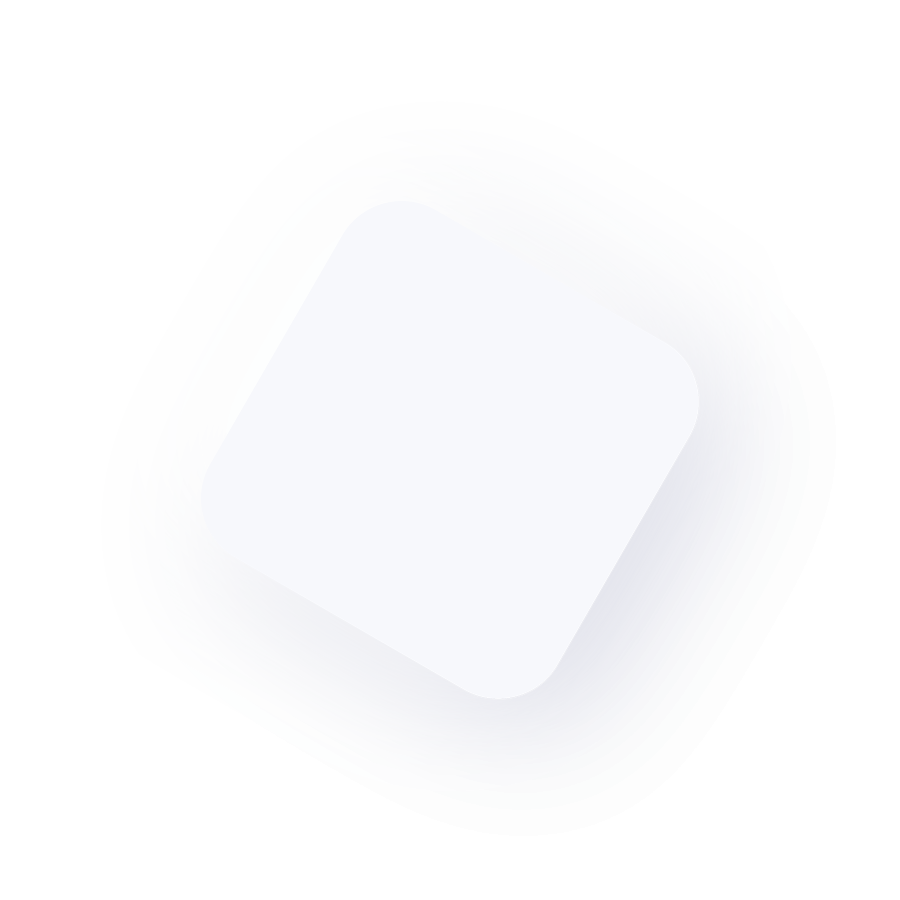
CASE STUDY:
Reducing Mold Costs
CLIENT:
German company operating in the lighting sector.
THE CHALLENGE:
The company approached us with a request to design nine new molds for the production of various plastic semi-finished products to expand their catalog.
VPLAST SOLUTION:
Since the nine requested molds were intended for manufacturing items of similar weight and shape, our team of technicians designed a single mold with nine different cavities, enabling the production of various plastic semi-finished products using the same mold.
Our consultancy went beyond what was initially requested. In fact, we suggested that the client not only supply the plastic components but also package them with screws, as specified by the client, in dedicated bags and labeled accordingly. This approach aimed to reduce the costs associated with packaging and assembling the molded parts.
CLIENT BENEFITS:
- 60% reduction in mold costs.
- Shorter lead times for mold production.
- Lower costs for the packaging and assembly of plastic components.