Case history
Optimization of Assembly Times for Production Lines and Elimination of Certain Pre-Assemblies
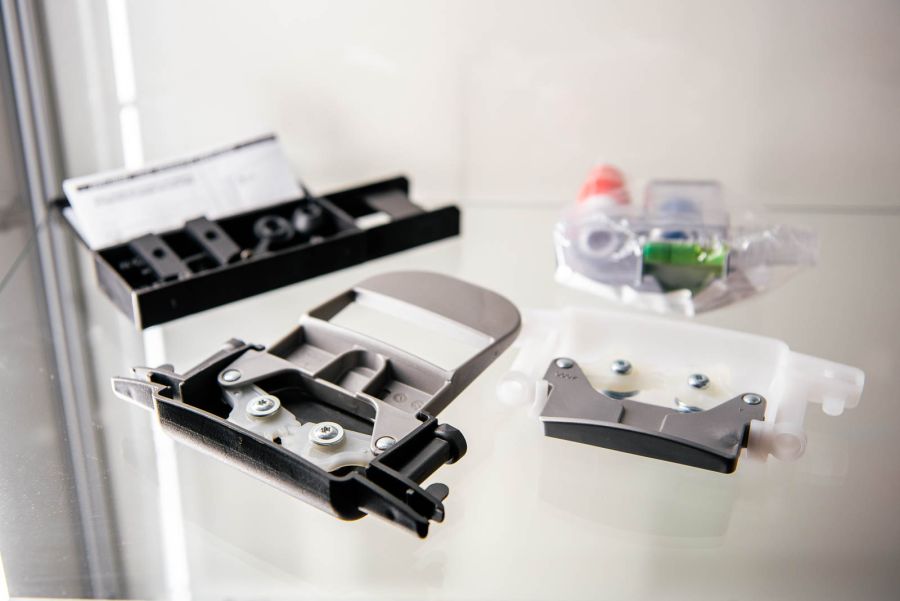
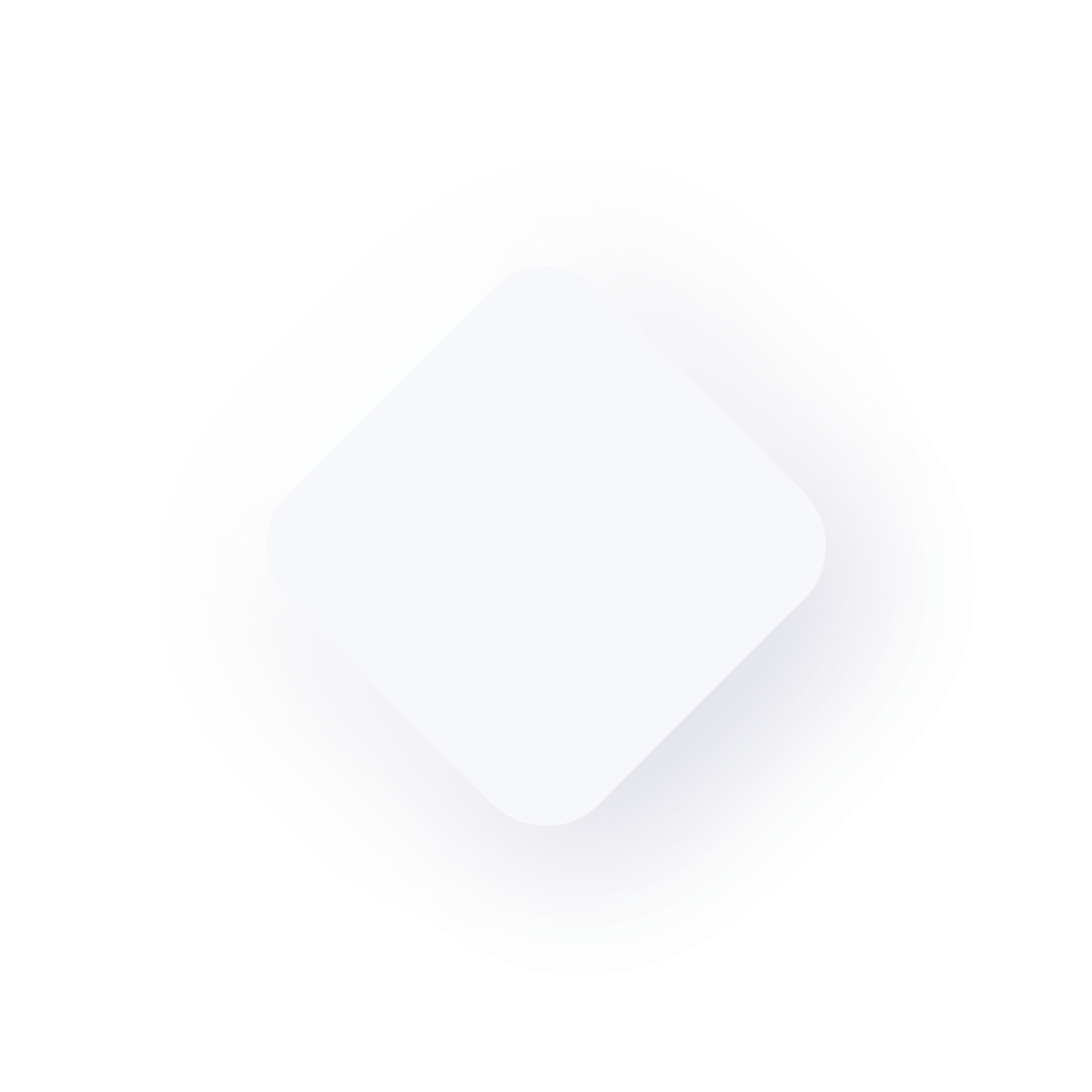
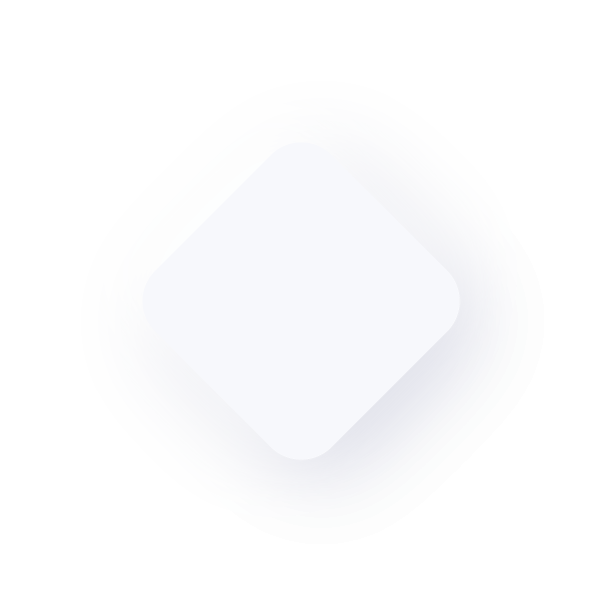
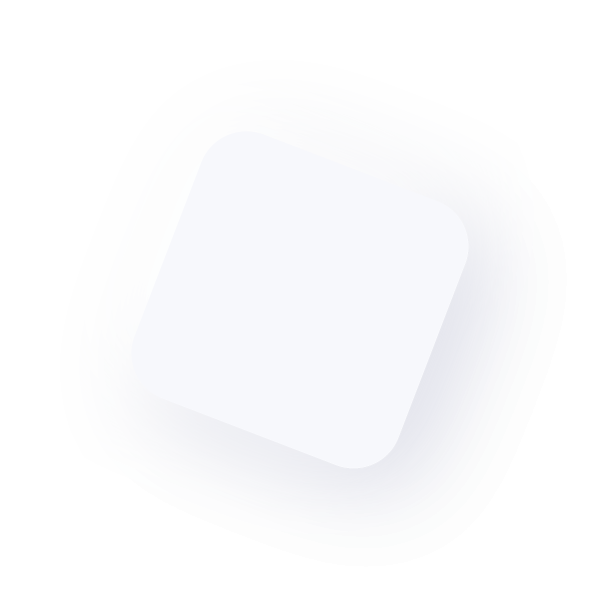
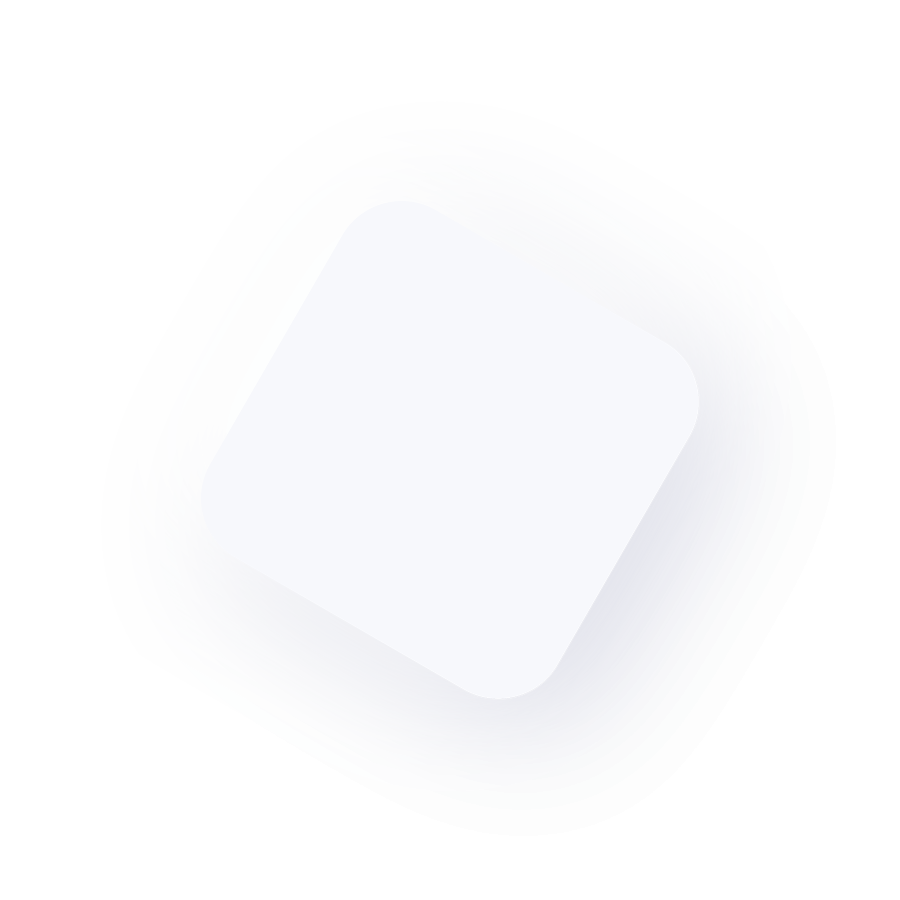
CASE STUDY:
Optimization of Assembly Times for Production Lines and Elimination of Certain Pre-Assemblies
CLIENT:
A company in the baby stroller sector.
THE CHALLENGE:
The company, during a review of its production processes following lean production methodologies, approached us to provide a solution to optimize the assembly times of certain production lines by eliminating some pre-assembly steps.
VPLAST SOLUTION:
To optimize assembly times, we first took over all the molds previously distributed among different suppliers. We then set up partnerships with suppliers for the direct procurement of some semi-finished products (e.g., screws, O-rings, etc.) and integrated pre-assembly lines in-house, creating stock inventories ready for reorder as agreed with the client.
Moreover, in line with reducing environmental impact, we opted for reusable plastic packaging, thereby optimizing warehouse space as well.
CLIENT BENEFITS:
- Reduction in time and management costs for various suppliers and products.
- Reduction in work times.
- Reduction in space dedicated to pre-assembly areas.
- Reduction in box usage.