Case history
Eliminating Non-Conformities Due to Acetal Shrinkage in Post-Production
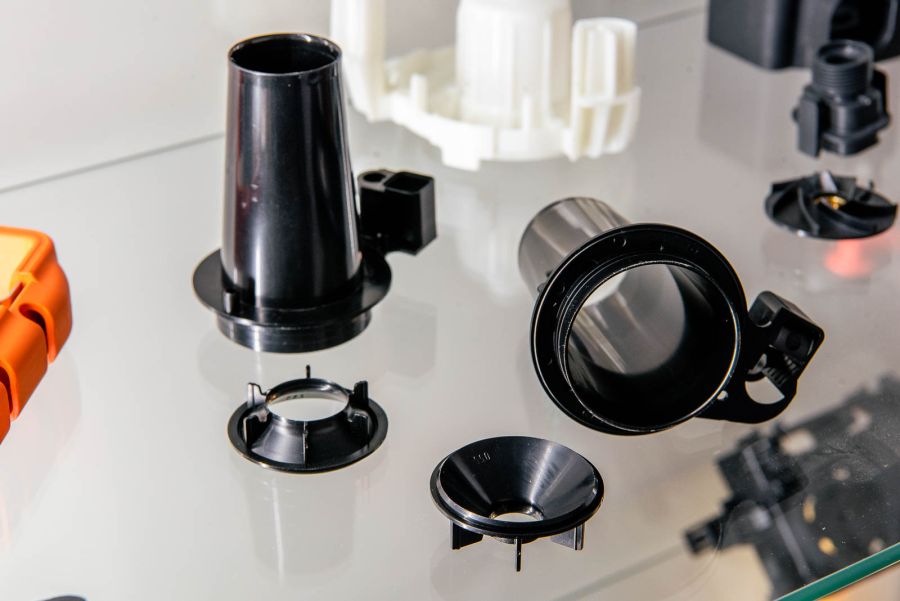
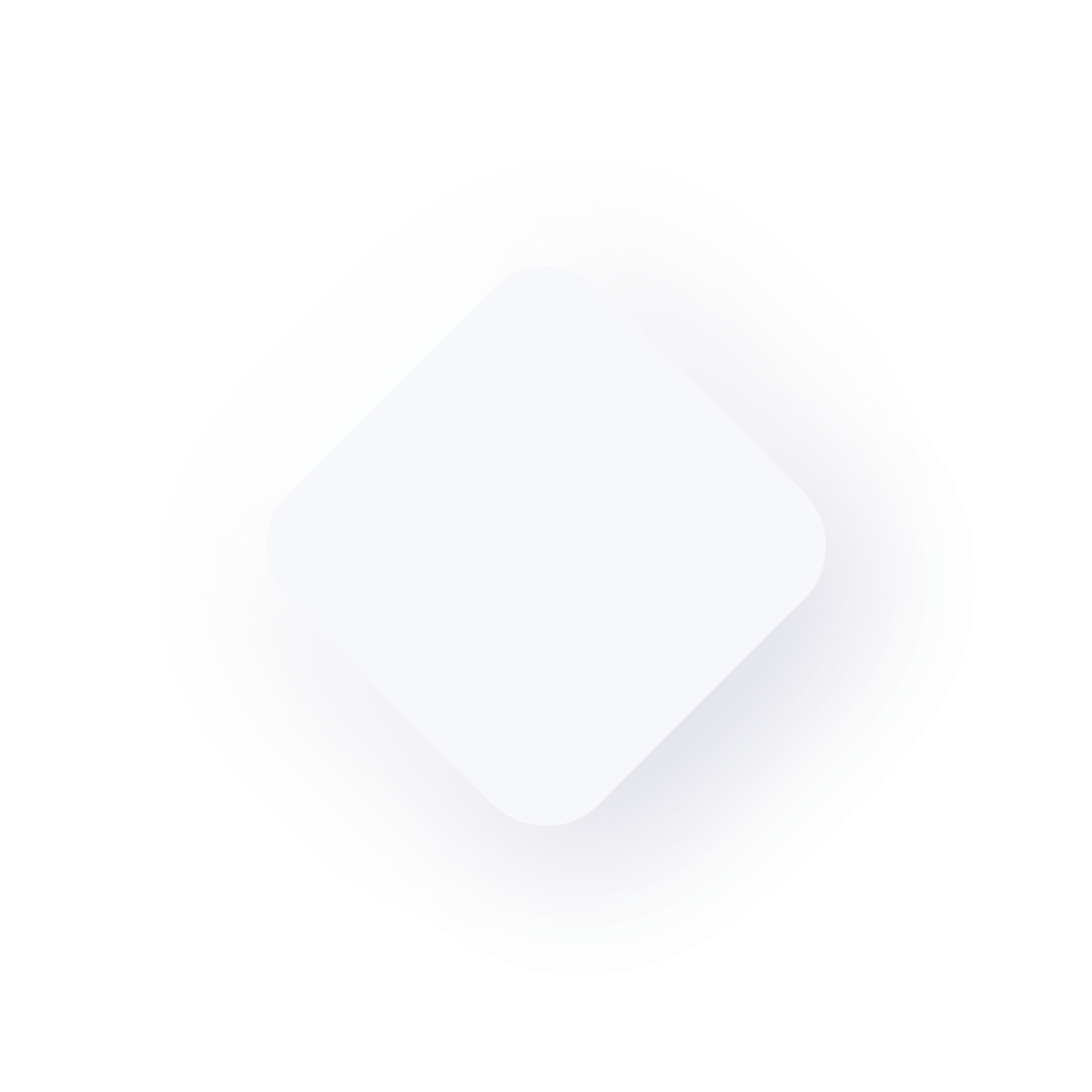
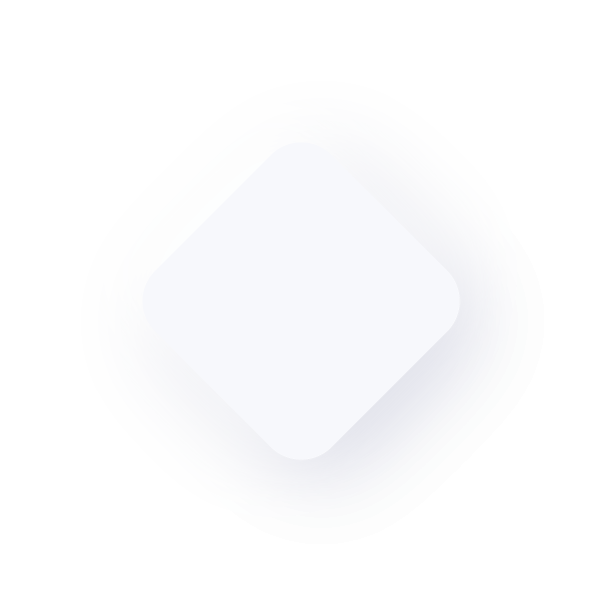
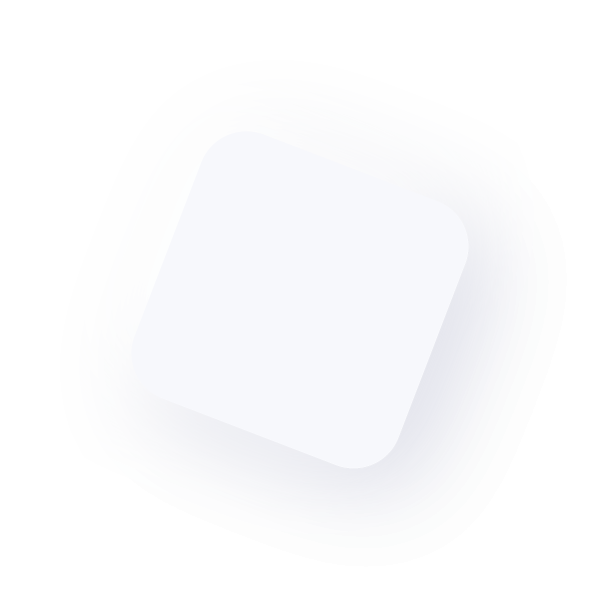
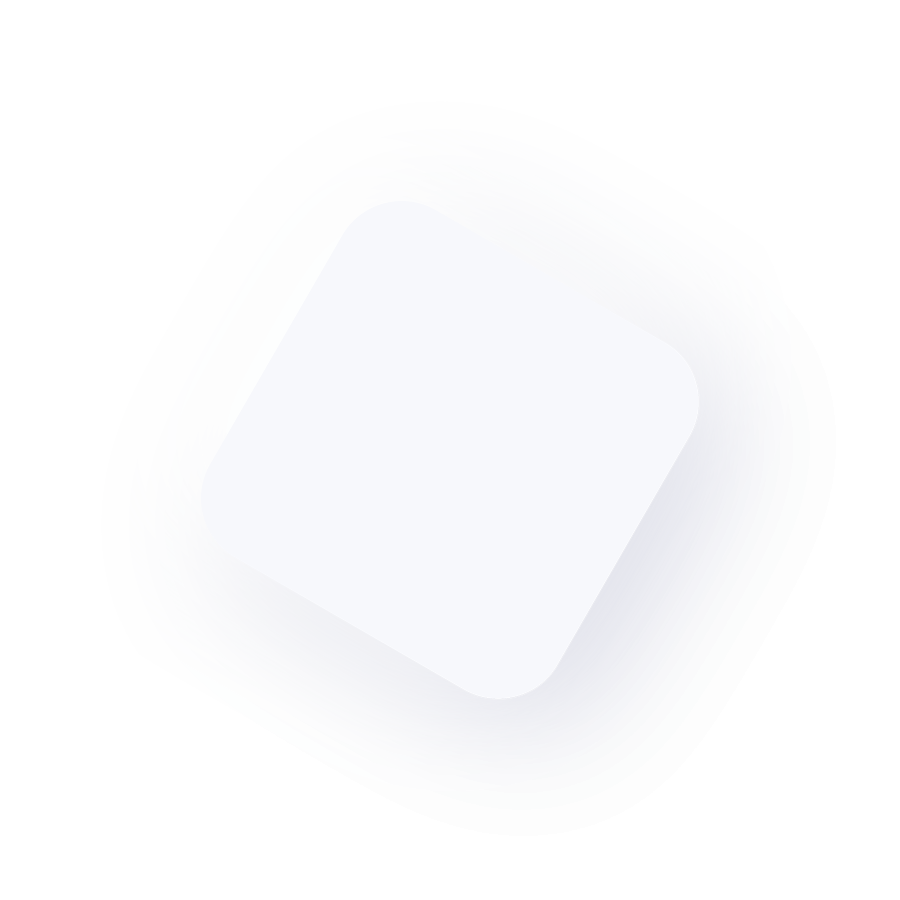
CASE STUDY:
Eliminating Non-Conformities Due to Acetal Shrinkage in Post-Production
CLIENT:
A multinational company in the boiler industry.
THE CHALLENGE:
The company reached out to us regarding an issue in their fume discharge system during boiler testing, caused by the height of a plastic semi-finished component. They requested a test batch to evaluate if the existing mold could ensure adherence to tolerances in 100% of production.
VPLAST SOLUTION:
We analyzed the issue before starting the test batch, identifying that the height non-conformity of the semi-finished plastic component was due to the shrinkage of the acetal material used in molding. Acetal can shrink during post-production if the mold temperature is not correctly set.
This issue had not been detected by the previous supplier during in-process production controls, as the non-conformity only appeared post-production. During the sampling phase, we conducted a process capability analysis on the height of the plastic semi-finished part to monitor the post-production shrinkage of acetal under different processing parameters.
The measurements, performed in-house using a statistical sampling method, allowed us to track the shrinkage behavior over time as it varied with mold temperature. After statistically determining the machine parameters needed to meet the client’s 100% tolerance requirement, these parameters were approved and saved for future production batches.
CLIENT BENEFITS:
- Zero non-conforming boilers during testing due to semi-finished component issues.
- Elimination of rework costs related to non-conforming plastic components.
- No additional costs to revise the existing mold.